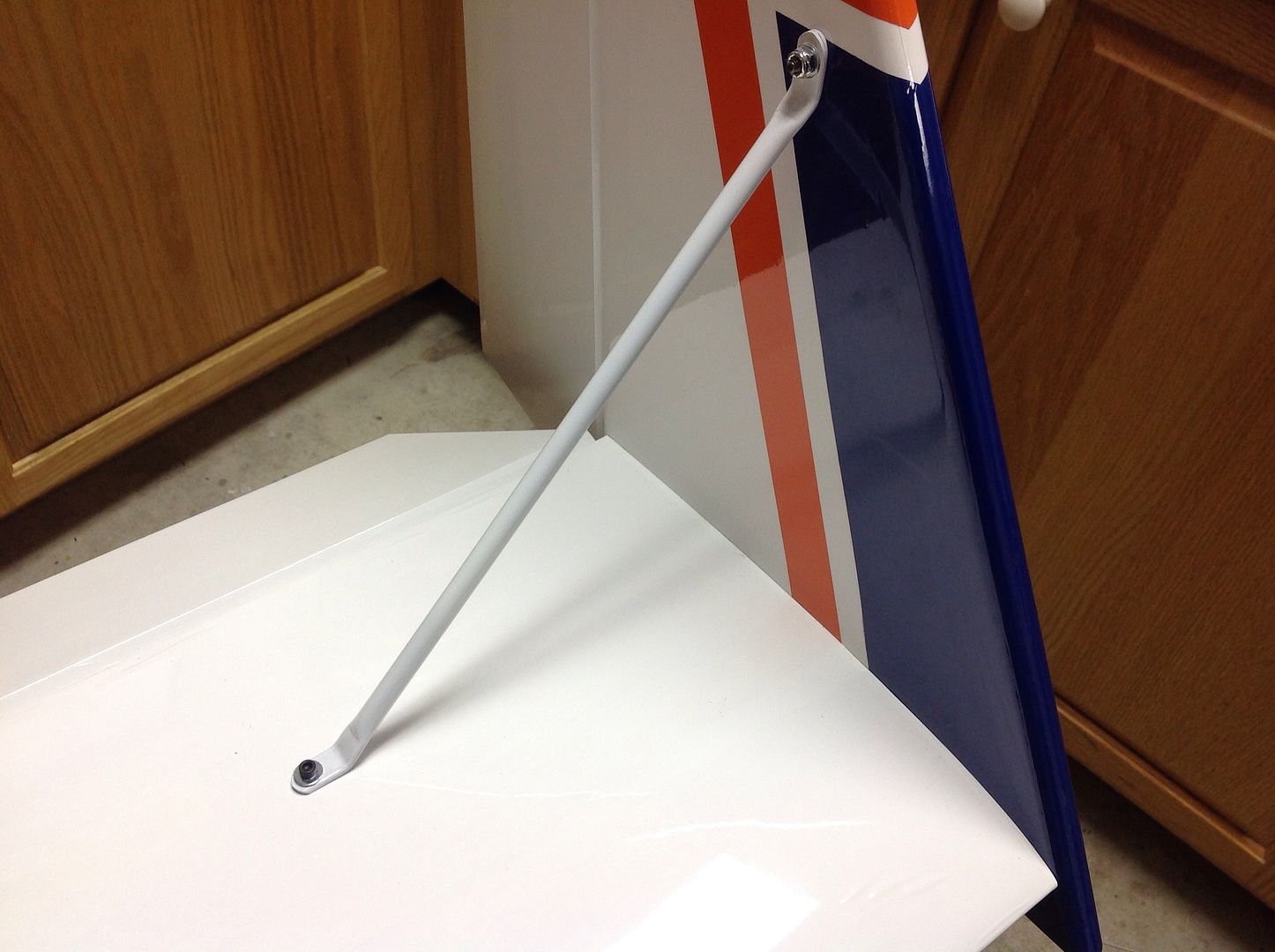
Hinges were epoxied in with West Systems G-Flex epoxy which holds extremely well and resists vibration damage.
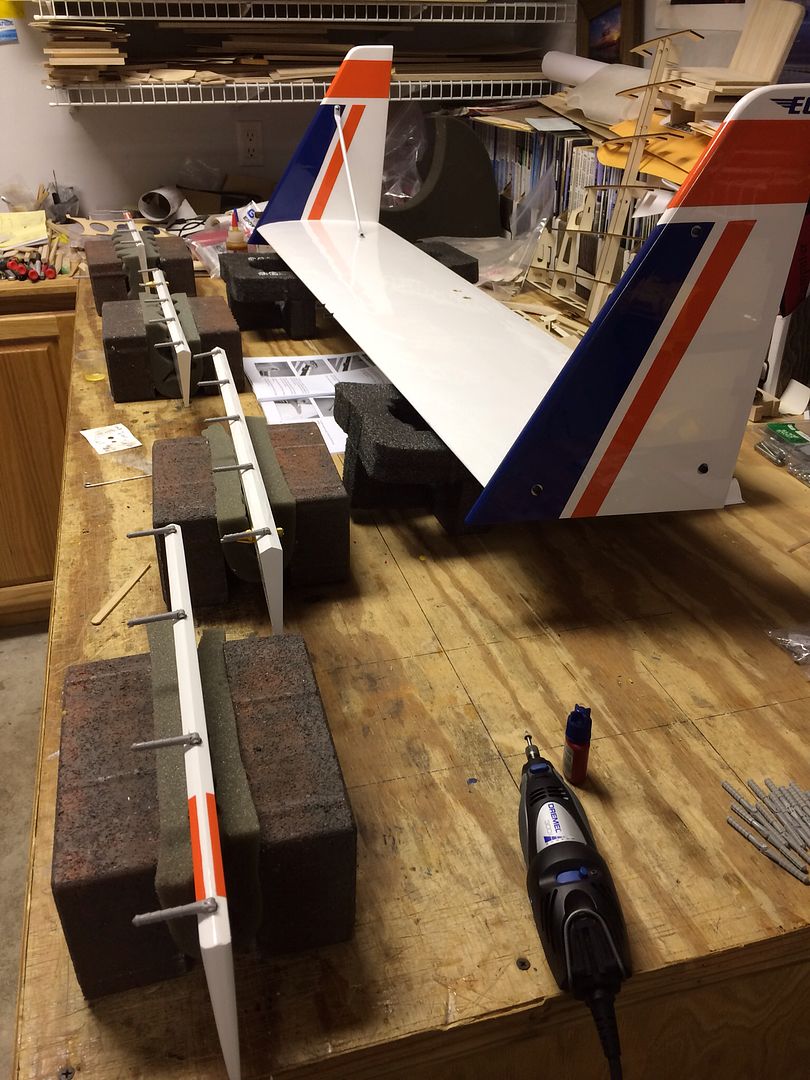
Our rudder servos were mounted to the stab instead of the covers.
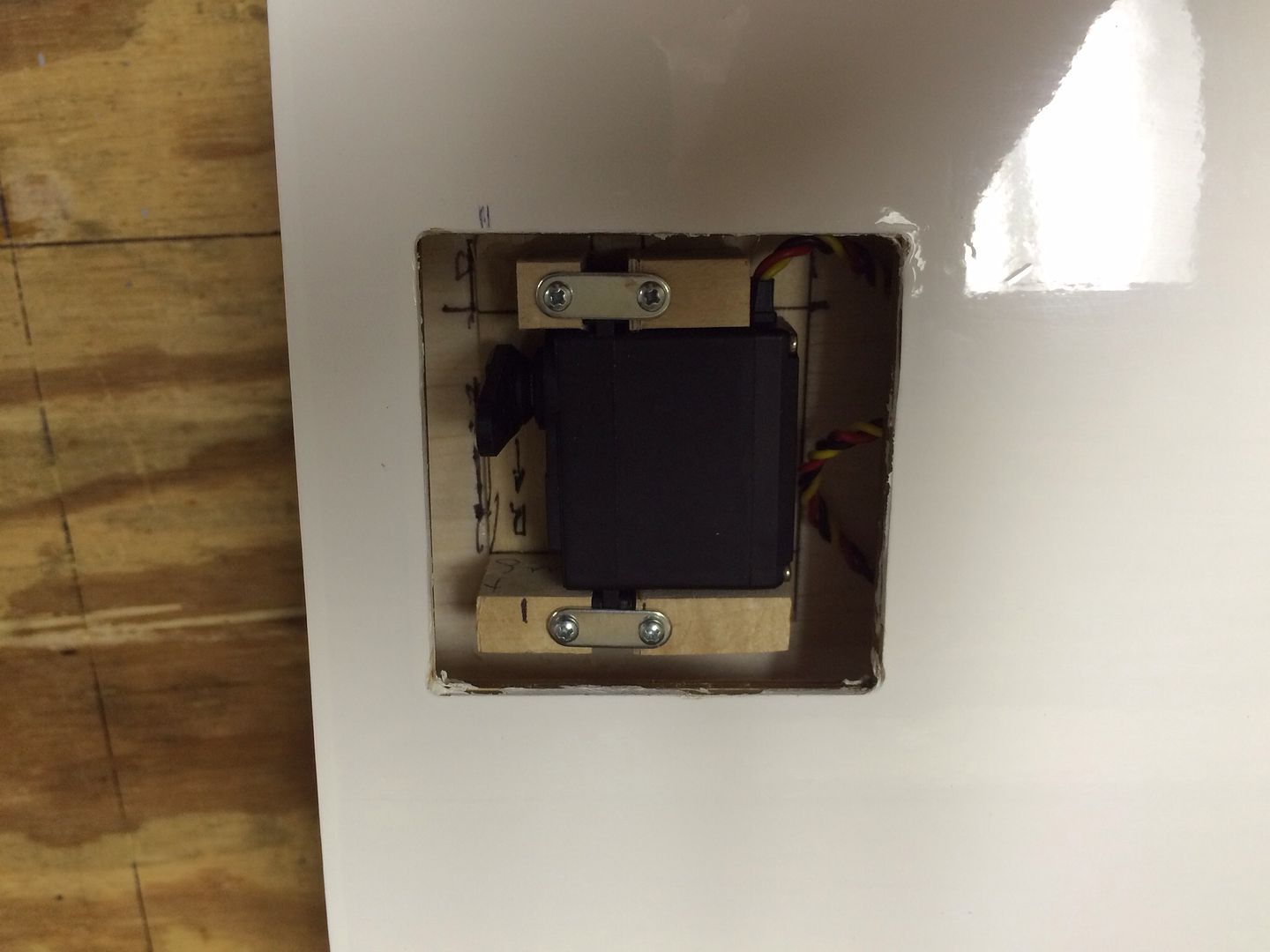
DuBro horns were used instead of the stock parts.
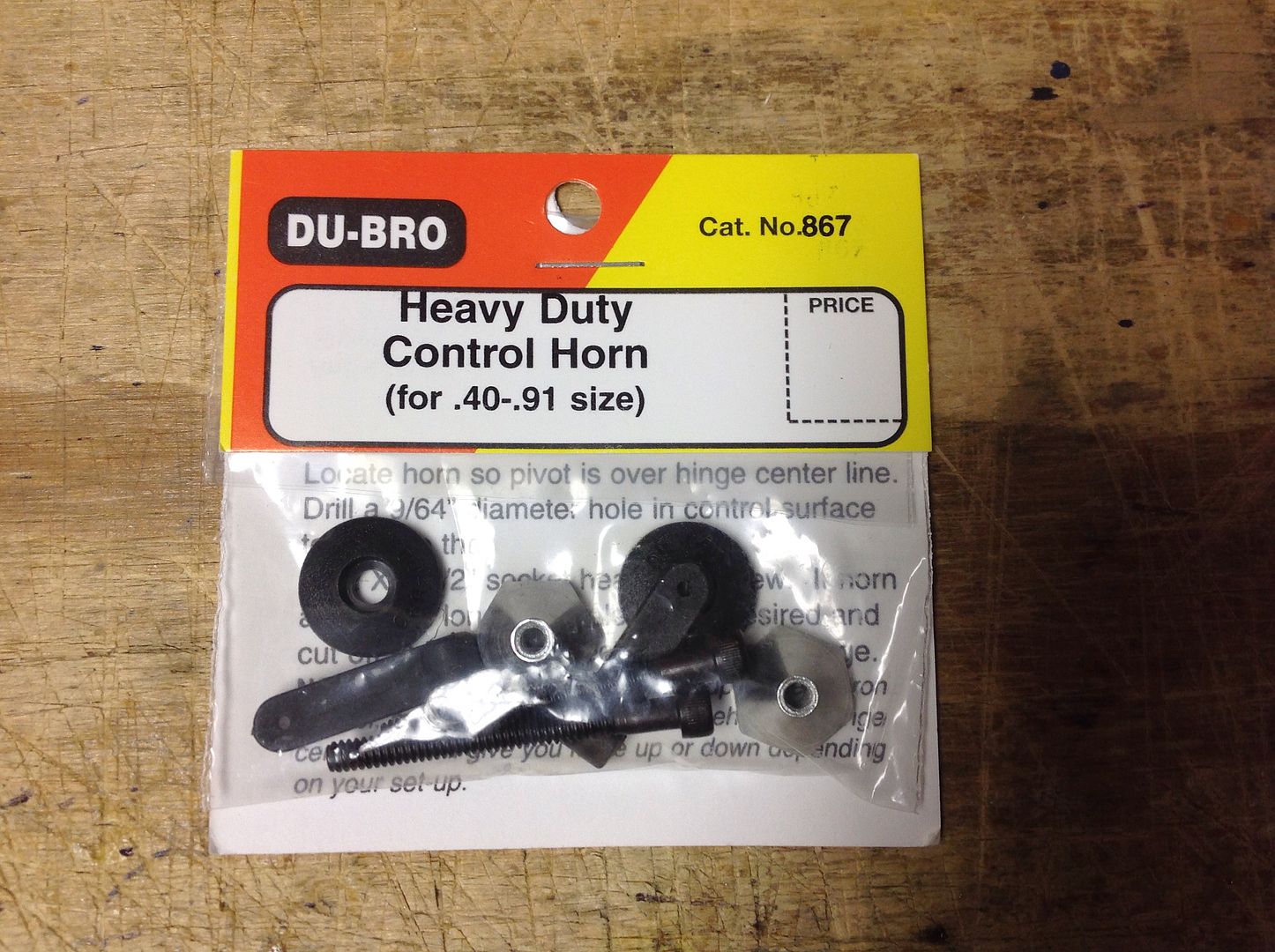
The supplied bolts are 1-1/2" long, but we changed them out to 2" long bolts for better control hookup geometry.
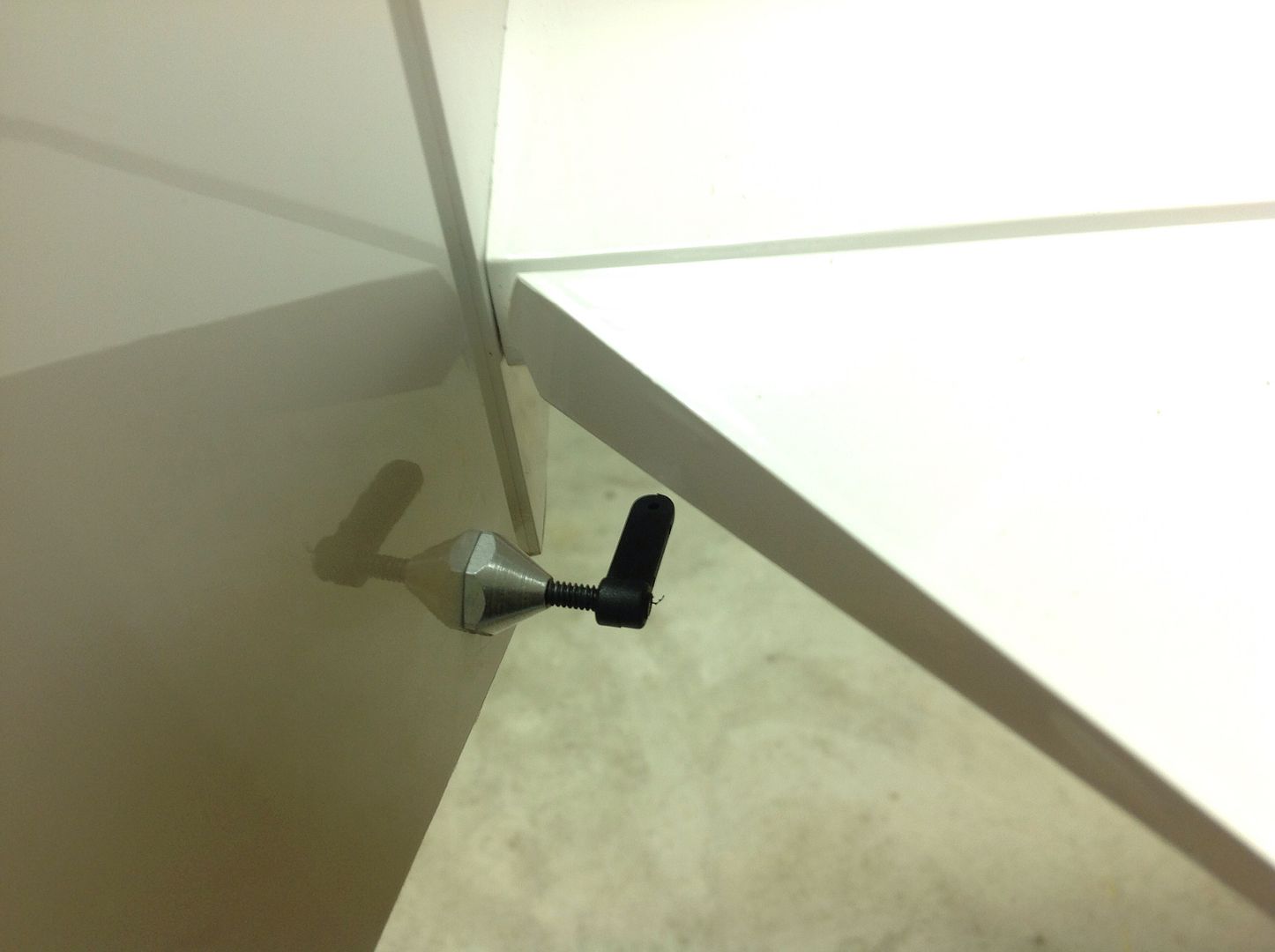
Leave a comment: